I don't have any of the replacement parts needed to rebuild the axle, so I thought I would go ahead and just clean up the exterior and then separate the hubs, remove the brakes and give the inside of the hubs a little spring cleaning. It will then make the whole business of replacing oil seals and installing new brakes so much easier and somewhat cleaner.
So, I spent last weekend getting frisky with wire brushes of all different shapes and sizes, as well as various flat headed screwdrivers chiseling mud, grease and downright gunk out of crevices and such.
 |
Before the makeover: notice the small pile of dirt below from chiseling away with a screwdriver before getting serious. |
Now, as a warning to all before scrolling down, let it be known, said and heard that this probably isn't going to be the most glamourous post of this amazing how to build a jeep in a lifetime story. This is basically being Charlie Brown's friend, Pigpen, on the driveway and cleaning up a big, nasty jeep part. I do have a lot of pictures (of dirty and clean metal parts) to razzle and dazzle you. Also, I did uncover a nifty secret that this axle has stowed away beneath layers and layers of crud. So, if you are down, lets scroll...
I'm going to hit you with my big news, first. I know, I should have held out until nearer the end, but what the heck...here it is...
 |
This is a close up of the left hand mounting tab of the axle. It is located above the orange jack stand in the previous picture. |
See it??!! Yes, that is a fancy script "F" mark made by the Henry Ford Company. In WWII, Ford produced almost as many jeeps as Willys. The jeep history is very convoluted, but the jist of it is it was an original Bantam design that was then modified by Willys. Willys could not produce enough jeeps as the military needed during the war, so Ford got a piece of the pie as well as a copy of the blueprints. Ford then tweeked the design a bit, yet was able to keep all parts interchangeable between the Ford (affectionately known as a GPW) and Willys (MB model) jeeps. Ford was notorious for stamping all of his products. I do not know the official reasoning behind this, but one of the many believable rumors is that Ford did not want a defective non-Ford part ever being attributed to coming from his factory. So, like writing my 5 year old's name in all of his clothing, Ford stamped various versions of "F's" on most of his parts. As the war progressed, he toned it down somewhat, but they are still plentiful. When I restored my first jeep, which is a GPW, I became very addicted to finding the F's on all of its parts. It is something most people with a Ford jeep will end up doing, no matter how hard they try to resist.
Needless to say, when I found this tiny little script F mark, I became extremly excited. Yes, this does mean that this axle is NOT original to this jeep since it is a Willys MB model, but me being a GPW guy, I love it!
 |
Brake drum covered in history. |
 |
Same brake drum after a lot of elbow grease and a wire brush gave it a what for. |
 |
Same brake drum as in the previous picture. If you turn your head to the side, you can see another "F" mark. |
 |
And another "F" mark. |
 |
And yet, another, Ford mark. The manual states that GP 1125 is a Drum, Brake, 9". Just a little fun fact for you. |
 |
I just had to step back and admire. Here is my view. |
 |
Axle is primed. |
 |
I tried to get artistic with this shot. There is also another GP mark that the brightness of the sun is hiding. |
This drum is on the driver's side and it would spin freely. The opposite passenger's side drum had some sort of bind and would more often than not be quite difficult to turn. So, I opted for tackling the easier side first and leave the more difficult (passenger side) for Sunday's work. I removed the nuts that hold the axle shaft in place and pulled it out, which in turn gave me access to the oversized nut that keeps the bearings and more importantly, the hub in place. Inside, I was greeted by some really nasty old Greasy Bob grease.
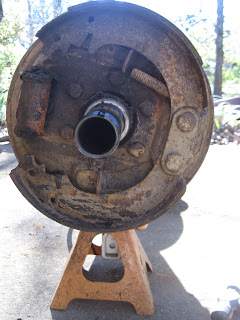 |
Here is what greeted me: two brake shoes (the crescent shaped pieces held by two large adjusting screws on the right hand side. On the left hand side, you can see the original Wagner wheel cylinder. Rebuild kits are available for these units, but I am opting to replace it entirely with a new cylinder. |
 |
Brake shoes and wheel cylinder removed. |
 |
So much for my cleanliness. The hub is off and the interior brake backing plate is exposed. Two nasty brake shoes are resting on the driveway. Those brakes are known to contain asbestos: not good in so many ways. |
I carefully cleaned out the hub and the brake backing plate so as to minimalize any dust particles going airborne. I taped off the center hole for the seals and bearings in the hub as well as the sides where the brakes will press against and primed the remaining exposed metal. I also removed the brake backing plate from the axle and primed it, too. While everything was disassembled, I ran all of the nuts and bolts through my wire brush spinning wheel and then rethreaded and tapped them all so as to make the installation so much easier.
 |
When everythig is installed, these gorgeous little bolts will never be seen. They are used to hold the brake backing plate to the axle, but the "F" marked heads are inside the hub and the nuts are on the outside. |
 |
This is the original oil seal. At the top, you can clearly see Henry's script "F".
Unfortunately, this is one of the parts slated to be removed and replaced with a modern seal. I'm going to try my best to remove it without destroying it. I think it is a small, but unique, piece of history. |
 |
A close up of the previous seal. |
 |
Same seal. Just more beauty in the details. |
 |
Interior of the brake backing plate cleaned, primed, and reinstalled. In an effort to keep dirt and crud out of the area where the axle shaft sits, I placed a wadded up paper towel. |
The following day, I did the same process to the other side of the axle. Everything was pretty much a repeat except for trying to separate the hub from the backing plate. For some reason, the brake shoes had expanded and were stopping the hub from spinning. I struggled and struggled trying to separate them. I couldn't do it. I thought, perhaps, that it might be easier to separate them if I removed the backing plate from the axle thus giving each piece room to move away from the other. I thought it was a genius thought...it was so genius that it reaked of ingenius. Kind of like the Three Amigos, it is infamous and more than genius. Well, often what appears to be perfect iin theory fails to develop in reality. At first I didn't see any immediate positive results. I think at the peak of my insanity, I had three flat head screwdrivers wedged in various sides along with my Fu-Bar. In the end, I removed the two nuts from the two large bolts that hold the brake shoes to the backing plate. These are the two biggest bolts you see on the right hand side of the above picture. I then tapped them into the hub, thus releasing the brake shoes. Then, the hub ceased its resistance and finally separated. I'll have to remember that one for next time. After that, it was business as usual and I repeated everything that I did from the other hub.
 |
This is the cleaned up backing plate for the passenger side. |
Afterwards, I fitted the cleaned up hubs back on, minus the old brake shoes. Again, this is something that I have ordered and will replace. The axle shaft went back in and everything was tightened up, but maybe not in that order.
And then I got curious to see what was inside the differential, or what I sometimes call the pumpkin in the middle of the axle. I needed to look inside for any broken, chipped or pitted gears and teeth so I could figure out what parts needed to be ordered. On one hand, I didn't want to look because then I would know. Like that reasoning makes any sense at all!? Anyhow, I removed and cleaned all of the bolts that hold the cover plate in place and peaked inside. Miraculously, everything looked really good...at least for what I could see. I spun the pinion gear for awhile and watched all of the gears rotate. It looked very similiar to the inside of a clock. Everything seemed to be well in order, which was a welcomed relief!
 |
Cover off and looking in... |
 |
...and finding more "F's" and GP marks! Can you see the tiny script F's left and right on the small clips between the bolts? |
 |
This one is on the inside of the cover plate. |
Satisfied with what I found, I reinstalled the cover plate. The last thing I did was to then loosen both the oil filler bolt and the oil drain bolt. Now, all I can do is sit back and wait for the new wheel cylinders, brake shoes, seals and gaskets to arrive.